Key Elements of Implementing MES for Continuous Improvement in Manufacturing
MES implementation for continuous improvement in manufacturing requires careful consideration of key elements to ensure success. Firstly, thorough planning and alignment of MES goals with overall business objectives are essential. This involves defining clear performance metrics, outlining project timelines, and establishing communication channels for all stakeholders involved in the implementation process.
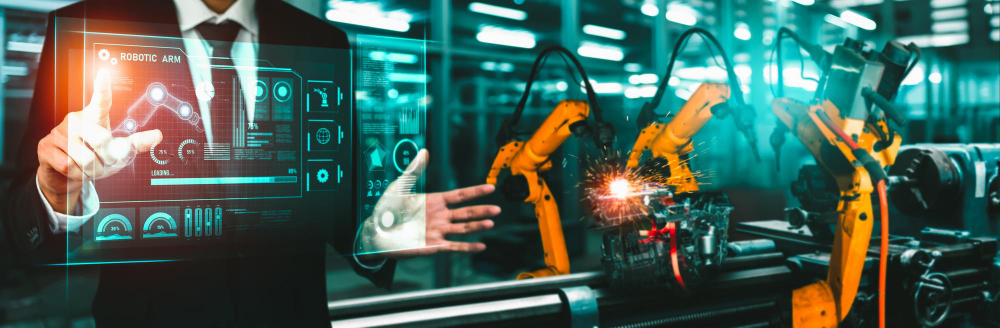
Additionally, selecting the right MES solution that fits the specific needs of the manufacturing environment is crucial. The chosen MES system should be scalable, user-friendly, and able to integrate seamlessly with existing manufacturing systems. Training and upskilling employees on how to effectively use the MES software is also paramount for successful implementation and utilization. By focusing on these key elements, manufacturers can maximize the benefits of MES for continuous improvement in their operations.
The Role of MES in Driving Operational Excellence
Manufacturing Execution Systems (MES) play a crucial role in driving operational excellence within manufacturing facilities. By providing real-time visibility into production processes, MES enables organizations to make informed decisions promptly and optimize their operations efficiently. MES systems act as a central hub for capturing and analyzing data from various stages of production, allowing companies to identify bottlenecks, streamline workflows, and improve overall efficiency.
Furthermore, MES facilitates effective communication and coordination between different departments, ensuring seamless integration of processes and alignment towards common goals. Through automated workflows and task management capabilities, MES helps in standardizing procedures, minimizing errors, and enhancing collaboration across the manufacturing floor. By enabling data-driven decision-making and fostering a culture of continuous improvement, MES serves as a catalyst for achieving operational excellence and driving sustainable business growth.
Benefits of Utilizing MES for Continuous Improvement
Utilizing Manufacturing Execution Systems (MES) offers a myriad of benefits for companies seeking continuous improvement in their manufacturing processes. One of the key advantages is the enhanced visibility into real-time production data, allowing for better decision-making and quick identification of bottlenecks or inefficiencies in the workflow. By having access to accurate and up-to-date information, organizations can streamline their operations, reduce downtime, and ultimately improve overall productivity.
Furthermore, MES enables better quality control through the standardization of processes and the implementation of automated data collection. With this system in place, manufacturers can track product quality at each stage of production, ensuring that any defects or deviations from quality standards are detected and addressed promptly. This results in higher-quality products, increased customer satisfaction, and ultimately, improved profitability for the business.
Challenges Faced in Implementing MES for Continuous Improvement
One of the main challenges faced in implementing MES for continuous improvement in manufacturing is the resistance to change from employees. Transitioning to a new system can be met with apprehension and reluctance, as employees may be comfortable with their current methods and fear the unknown. This resistance can hinder the adoption and effectiveness of the MES system, making it crucial for management to communicate the benefits and provide proper training to address any concerns.
Another challenge is the integration of MES with existing systems and technologies within the manufacturing facility. Ensuring seamless communication and compatibility between various systems can be complex, especially in older facilities with outdated infrastructure. This integration process requires thorough planning and coordination to avoid disruptions to operations and to maximize the capabilities of the MES system for continuous improvement efforts.
Strategies for Successful Implementation of MES in Manufacturing
Implementing MES in manufacturing requires careful planning and execution to ensure a successful outcome. One key strategy is to involve all stakeholders from different departments right from the beginning of the process. This collaboration promotes a better understanding of each team’s needs and fosters a sense of ownership and commitment to the MES implementation project. Additionally, having clear communication channels and regular updates throughout the implementation phase can help address any issues promptly and keep everyone informed of progress.
Another crucial strategy for successful MES implementation is to conduct thorough training and development programs for all employees who will be using the system. Providing comprehensive training ensures that staff are equipped with the necessary skills and knowledge to effectively utilize the MES platform. Moreover, ongoing support and guidance post-implementation are essential to address any challenges that may arise and to continuously improve the utilization of MES for optimal results.
• Involving all stakeholders from different departments
• Clear communication channels and regular updates
• Thorough training and development programs for employees
• Ongoing support and guidance post-implementation
The Impact of MES on Overall Efficiency and Productivity
When it comes to manufacturing operations, the implementation of Manufacturing Execution Systems (MES) can have a profound impact on overall efficiency and productivity. By providing real-time visibility into production processes, MES enables manufacturers to identify bottlenecks, streamline operations, and optimize resource utilization. This leads to increased efficiency in production workflows, reduced downtime, and improved throughput.
Furthermore, MES systems play a crucial role in enhancing productivity by enabling manufacturers to track key performance indicators (KPIs), monitor work orders, and analyze production data in order to make data-driven decisions. These insights help in identifying trends, predicting potential issues, and proactively taking corrective actions to ensure smooth operations. As a result, organizations can achieve higher productivity levels, meet production targets, and ultimately drive operational excellence.
Case Studies Highlighting Successful MES Implementations
In a manufacturing setting, the successful implementation of Manufacturing Execution Systems (MES) has proven to be a key factor in driving operational efficiency and continuous improvement. One notable case study involves a large automotive manufacturer that integrated MES to streamline production processes and enhance data visibility across all operational areas. By utilizing MES, the company was able to optimize resource utilization, reduce downtime, and improve overall production output significantly.
Another compelling case study comes from a leading electronics manufacturer that successfully implemented MES to track and manage the production lifecycle of their products. Through real-time monitoring and feedback mechanisms provided by MES, the company was able to identify inefficiencies in their manufacturing processes promptly and make data-driven decisions for process improvement. As a result, the company experienced notable cost savings, improved product quality, and enhanced overall operational performance, showcasing the transformative impact of MES on manufacturing operations.
The Importance of Data Analytics in MES for Continuous Improvement
Data analytics plays a crucial role within Manufacturing Execution Systems (MES) by providing manufacturers with actionable insights to drive continuous improvement. Through the capture and analysis of various data points, MES can identify trends, patterns, and inefficiencies within the manufacturing process. This allows for informed decision-making and targeted improvements to enhance overall operational efficiency and quality control.
Furthermore, data analytics in MES enables real-time monitoring of key performance indicators (KPIs) to track production performance and identify bottlenecks promptly. By leveraging data-driven insights, manufacturers can proactively address issues, optimize processes, and streamline workflows for increased productivity and cost savings. The ability to make data-driven decisions based on insights derived from data analytics is essential in today’s competitive manufacturing landscape.
Collaboration Between Departments for Effective MES Implementation
Collaboration between different departments within a manufacturing organization is imperative for the effective implementation of Manufacturing Execution Systems (MES). The success of MES integration depends on the seamless communication and alignment of goals between departments such as production, quality control, maintenance, and IT. Without open collaboration and cross-functional teamwork, the full potential of MES in driving operational excellence and continuous improvement cannot be realized.
When departments work in silos, there is a risk of inefficiencies, data discrepancies, and implementation delays. By fostering a culture of collaboration, organizations can ensure that the MES implementation process is streamlined and that each department’s unique insights and expertise are leveraged effectively. Clear communication channels and regular meetings between departments help to address challenges proactively, identify opportunities for improvement, and ensure that the MES serves the needs of the entire organization, not just individual departments.
Training and Development for MES Utilization
Training and development play a vital role in ensuring the successful utilization of Manufacturing Execution Systems (MES) in manufacturing operations. Employees must undergo comprehensive training to understand the intricacies of MES software and how it can improve their daily tasks and overall processes. This not only enhances their technical proficiency but also increases their confidence in utilizing MES effectively, leading to maximized benefits for the organization.
Continuous development is equally important as technology evolves and new features are introduced within MES platforms. Offering regular training sessions and refresher courses can keep employees up-to-date with the latest advancements in MES technology and practices. By investing in the ongoing development of staff members, companies can foster a culture of continuous improvement and innovation, driving efficiency and productivity across the manufacturing floor.
Utilizing Real-time Monitoring and Feedback for Continuous Improvement
Real-time monitoring and feedback are essential components for driving continuous improvement in manufacturing processes. By implementing systems that provide instantaneous data on production metrics, companies can quickly identify areas for improvement and take immediate corrective actions to enhance efficiency and productivity. This real-time visibility into operations allows for proactive decision-making and enables organizations to stay agile in responding to changing demands and market conditions.
Furthermore, leveraging real-time feedback mechanisms can facilitate better communication and collaboration among cross-functional teams within a manufacturing environment. By sharing instant updates on key performance indicators and performance metrics, departments can work together seamlessly to address bottlenecks, streamline processes, and drive overall operational excellence. This collaborative approach, guided by real-time data insights, fosters a culture of continuous improvement and empowers employees at all levels to contribute proactively to enhancing manufacturing operations.
Integration of MES with Other Manufacturing Systems
Integration of MES with other manufacturing systems is crucial for streamlining operations and enhancing efficiency within a manufacturing environment. By seamlessly connecting MES with systems such as ERP and PLM, organizations can achieve a more synchronized and data-driven approach to production processes. This integration allows for real-time data exchange, enabling quick decision-making and better coordination between different departments.
Moreover, integrating MES with other systems like SCADA and CMMS can further optimize maintenance activities and production scheduling. This interoperability ensures that all aspects of the manufacturing process work together harmoniously, leading to improved overall performance and reduced downtime. The ability to integrate MES with various manufacturing systems not only enhances visibility and control but also paves the way for a more agile and responsive operational framework.
Future Trends in MES for Continuous Improvement in Manufacturing
Moving forward, future trends in Manufacturing Execution Systems (MES) for continuous improvement are rapidly evolving to meet the demands of the digital era. One key trend to watch out for is the increasing integration of MES with advanced technologies such as artificial intelligence (AI) and machine learning. By harnessing the power of AI, MES can make real-time data analysis more efficient, leading to proactive decision-making and predictive maintenance strategies.
Furthermore, the adoption of cloud-based MES solutions is gaining momentum in the manufacturing industry. Cloud-based MES offers scalability, flexibility, and accessibility, allowing manufacturers to easily deploy and manage their systems across multiple facilities. This trend not only promotes real-time collaboration and data sharing but also enables manufacturers to leverage the benefits of remote monitoring and control for enhanced productivity and operational efficiency.
Additional Resources:
[catlist categorypage=”yes”]
[newsletter]
Table of Contents
Categories:
[categories orderby=name]
Latest Posts:
[sbs_latest_posts]
FAQs:
What are some key elements to consider when implementing MES for continuous improvement in manufacturing?
Key elements to consider include data analytics, real-time monitoring, integration with other systems, and collaboration between departments.
How does MES drive operational excellence in manufacturing?
MES helps streamline processes, improve efficiency, enhance productivity, reduce waste, and enable better decision-making through real-time data.
What are some benefits of utilizing MES for continuous improvement in manufacturing?
Benefits include improved efficiency, increased productivity, reduced costs, enhanced quality, better decision-making, and overall operational excellence.
What are some challenges faced in implementing MES for continuous improvement in manufacturing?
Challenges may include resistance to change, lack of training and expertise, integration issues, data security concerns, and cultural barriers.
What are some strategies for successful implementation of MES in manufacturing?
Strategies include proper planning, clear communication, stakeholder engagement, training and development, pilot testing, and continuous improvement.
How does MES impact overall efficiency and productivity in manufacturing?
MES helps optimize processes, eliminate bottlenecks, reduce downtime, improve resource utilization, and enhance overall operational performance.
Can you provide examples of successful MES implementations in manufacturing?
Case studies showcasing successful MES implementations include companies that have significantly improved their efficiency, productivity, and quality through MES.
Why is data analytics important in MES for continuous improvement in manufacturing?
Data analytics help identify trends, patterns, and insights that can drive continuous improvement efforts, optimize processes, and enhance decision-making.
How important is collaboration between departments for effective MES implementation in manufacturing?
Collaboration between departments is crucial for aligning goals, sharing information, resolving conflicts, and ensuring a successful MES implementation across the organization.
How can training and development aid in utilizing MES for continuous improvement in manufacturing?
Training and development help employees understand the system, use it effectively, identify opportunities for improvement, and contribute to the overall success of MES implementation.
Why is real-time monitoring and feedback essential for continuous improvement in manufacturing?
Real-time monitoring and feedback enable quick decision-making, proactive problem-solving, immediate adjustments, and continuous optimization of processes in manufacturing.
How important is the integration of MES with other manufacturing systems for continuous improvement?
Integration with other systems allows for seamless data exchange, improved visibility, enhanced efficiency, and better decision-making, leading to overall operational excellence.
What are some future trends in MES for continuous improvement in manufacturing?
Future trends may include increased use of AI and machine learning, IoT integration, cloud-based solutions, predictive analytics, and digital twins to further enhance efficiency and productivity in manufacturing.